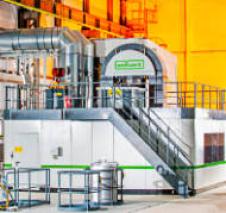
As the engineering and manufacturing supply chains emerge from the pandemic, plasma nitriding is again in significant demand for the heat treatment of new and replacement components. Responding, Wallwork Group are upping capacity with the addition this year of two further Rübig plasma nitriding furnaces, the first due for August.
Wallwork director, Simeon Collins, explained, "This is a further £650K investment by the group, this time in our Cambridge plasma nitriding centre, increasing the existing capacity to six operational plasma nitriders, providing 24/7 processing. We are also adding a new dedicated area for inspection of case depth, structure and other quality aspects of the nitriding process."
The Rübig furnace range chosen is the Micropuls Everest. This plasma nitrider offers several advantages, including three heating and cooling zones with the temperature measured directly at the component. A blast chiller shortens process times, while optimised filling and increased energy efficiency reduce running costs.
Nitriding is a metal heat treatment process that improves the endurance of wear parts such as gears, camshafts and followers, valve parts, aero-engine and airframe components, dies, extruder screws and injectors. In the Rübig nitrider, molecular nitrogen is cracked in plasma to obtain active nitrogen which then penetrates the component's surface. The process meets differing needs because the depth and properties of the case hardened layer can be finely controlled. Wallwork also design and manufacture the physical masking needed to ensure only the specified surfaces are exposed and hardened.
"The process has the major advantage of being relatively cool compared with other heat treatment methods. Importantly, this means the dimensions and characteristics of the base metal are not compromised. Also, it is ideally suited for low temperature plasma nitriding of stainless steels as it minimises potential loss of corrosion resistance in the metal, which could compromise its use in harsh environments," Simeon added.
There are no chemical residues and so the process can be followed by physical vapour deposition (PVD) coating to impart even better wear resistance for use in high-load applications. Cambridge, also being Wallwork's centre for advanced PVD coating technology, gives customers access to both plasma nitriding and coatings under one roof. Combined with the Group's dedicated transport fleet for pick-up and delivery anywhere in the UK, this ensures an efficient and quick turn-around customer service.
Wallwork holds extensive approvals from company, national and international accreditation bodies. With well-equipped laboratories to test and evaluate existing plasma nitriding methods and develop new single or duplex processes, the company has a wealth of real-world problem solving experience.
More Information
Simeon Collins, Director, Tel. +44 (0)161 797 9111
E-mail: simeon.collins@wallworkht.com Web: www.wallworkht.co.uk
Wallwork Group, Lord Street, Bury, Greater Manchester, BL9 0RE
Release issued: July 12, 2021
Browse Articles
< Previous |
Next >
Wallwork Group News Archive